15
Generation & Wholesale Markets
October/November 2013 www.esb.ie/em

REFURBISHMENT OF STACKER/RECLAIMER NO. 1 AT MONEYPOINT
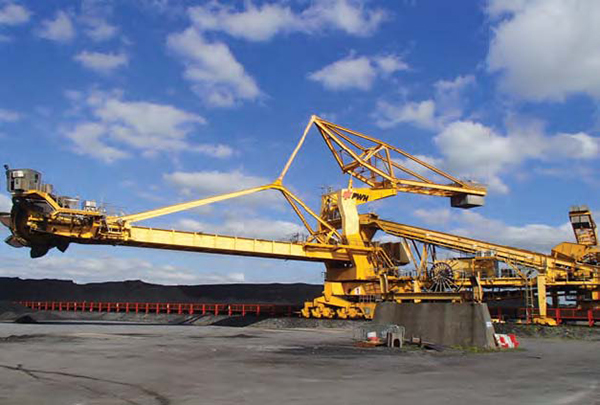
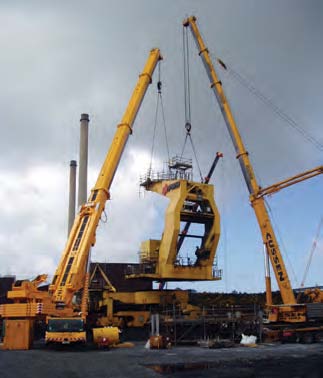
» On January 21st 2013 a fire occurred on Stacker/Reclaimer No.1 that engulfed the hoppers between the intermediate and yard belts.
THE STACKER was being operated at the time, but was evacuated safely. The function of the Stacker is to either stack coal from a ship or to reclaim the coal to send to the station as Money-point's primary fuel.
A project team was appointed by Coalyard Maintenance Manager Ciarán McManus and Refurbishment Project Manager Nigel Laffan with all project supervision carried out by Moneypoint's maintenance team members.
The entire machine had to be dismantled and 12 different contracting companies, excluding sub-contractors, have carried out various works from hydraulics and motor refurbishment, heavy lifting and re-machining. APC were appointed as mechanical contractor, with Mercury responsible for rewiring. Thyssen Krupp (OEM) had an advisor onsite for all mechanical work, while PBI, also had an advisor on-site for the electrical recommissioning works.
Much of the repair works completed were directly attributable to the fire, however other repairs were to remedy as founds and in particular corrosion damage.
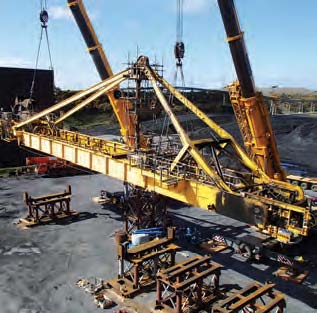
Following an intensive 23-week work programme the machine has successfully returned to service. The work by all parties in Money-point, not just those directly involved with the re-assembly of the machine, has to be acknowledged and commended. During this project there were zero LTIs, with over 22,000 man hours worked as well as the constraints on Moneypoint station to v operate near maximum output over the last number of months with one Stacker and reduced stock-I pile capacity and of course the un-planned nature and volume of the work.
Process Safety - central to ‘the new way we do business’
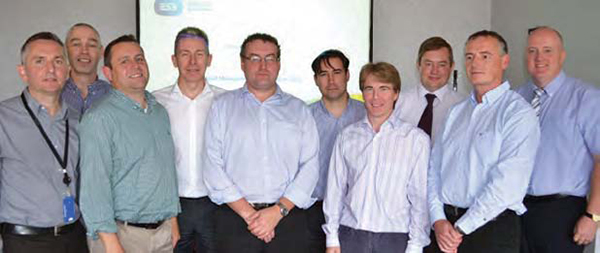
ESB HAS ALWAYS strived to increase the safety of its staff, contractors and the public by meeting and exceeding regulatory requirements, and by setting ever challenging targets for safety performance and injury prevention. Likewise, ESB has also endeavoured towards engineering and asset management excellence by setting high standards for the design, construction, operation and maintenance of our plants.
Process Safety was first identified in 2011 as a necessity for ESB Generation following a number of high-profile international incidents, the high-energy processes operated in our plants and more stringent standards being adopted across the industry.
Brian McAleer, Programme Manager, explains: “Process Safety is concerned with preventing harm to people, the environment and plant from the uncontrolled release of hazards and energy from engineering assets”.
A gap analysis carried out in 2012 identified a number of areas for improvement. Eight Process Safety improvement projects have now been prioritised for immediate delivery, with an additional six planned for 2014.
“We must adopt a more systematic approach to ensuring the integrity of our plant and giving assurance that our stations are safer places for all of us,” said Paddy Hayes, Executive Director and EDT Process Safety Programme Sponsor.
PROCESS SAFETY PROJECTS
PROCESS SAFETY PROJECTS The eight prioritised Process Safety projects were launched this September when the Project Managers were brought together to agree and discuss the programme roadmap, project methodology, challenges and delivery plans. The 8 prioritised and their project managers are:
• Alarm Management - Stephen Carrig
• Operational Log - Donal Brogan
• Staff Development and Safety Improvement - Harry Wisener
• Safety Critical Assets - Tomas Waters
• Incident and Audit Management - Darragh Duhy
• Hazard Identification and Risk Management - Michael Rocke
• Work Management Improvement- Alan Bane
• KPI Dashboard - Donal Brogan
ESB Trading go-live with new trading and risk management systems
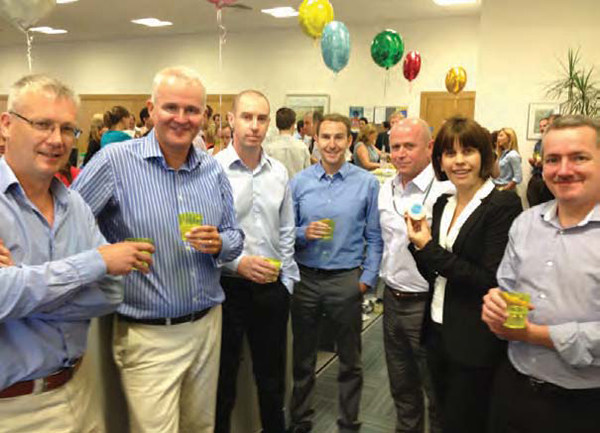
»On August 6th 2013 ESB Trading went live with release 1 of the Future Trading Project (FTP), which delivered a new trading and risk management platform.
FOR THE FIRST TIME, ESB now has the supporting systems and processes to trade its generation assets as a portfolio in the SEM market. Release 1 puts in place an integrated IT Trading Solution which is critical to supporting the delivery of our trading strategy and the foundation for further growth and development, especially in the UK market.
The FTP delivered a single Energy Trading and Risk Management system and supporting systems and processes for ESB Trading, and will support group-wide trading risk management at corporate level.
“The go-live of Future Trading Project Release 1 on August 6th is a fantastic achievement. The successful delivery of this significant and very complex project is a credit to all involved. There has been a tremendous amount of hard work, teamwork and effort by all involved,” commented Geraldine Heavey, Manager ESB Trading.
She added: “I would like to take this opportunity to congratulate everyone and again, say well done and thank you to everyone involved in making this happen.”
Release 1 delivers a flexible and scalable trading and risk management solution, including:
• All SEM-related trading in Power, Gas, Coal, Oil, Financials, Fx and Carbon
• Central position management for SEM trading activities
• Risk and Credit Management (VaR, Mark to Market, P&L, Credit Exposure)
• New portfolio fuel hedging analytics
• Confirmations and trade settlement
• New portfolio based trader
• Standard trade lifecycle controls
• Integrated market pricing and forward curve generation
• ESB group level position/risk management.
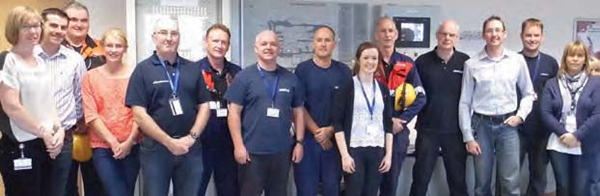
A YEAR AT COOLKEERAGH
PAULA DUNLOP, third-year Electrical Engineering undergraduate completed her year-out placement at Coolkeeragh at the end of August. Paula is one of a number of students in the Electric Ireland sponsored bursary programme run at Queen's University of Belfast. During her year at Coolkeeragh Paula worked on a number of valuable projects including a station Lightning Protection review and outage electrical maintenance support.