20

ENERGY INTERNATIONAL
December 2011/January 2012 www.esb.ie/em

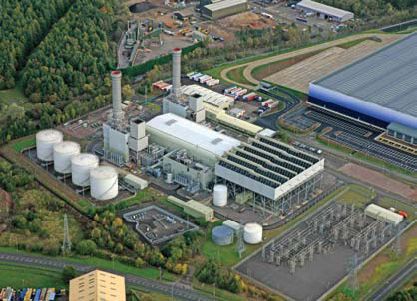
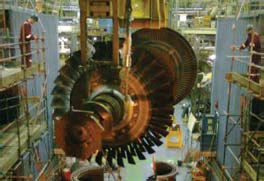
Successful major overhaul at Corby Power
CORBY POWER’S THIRD major overhaul in its 20 years of operation was successfully completed during the summer months of 2011.
The outage comprised major inspections of both gas-turbines, the steam turbine, the chemical cleaning of Heat Recovery Steam Generators (HRSG) and significant pressure part inspection and verifications in accordance with the Pressure Systems Safety Regulations (PSSR).
The overhaul also represented an opportunity to carry out preventative maintenance in accordance with the OEM guidance, and the station staff’s direct experience and intimate knowledge of the plant played a very important role in both delivery of the overhaul and preparation for the station’s next operating cycle.
Scope
All planned work was undertaken and all as-founds were addressed. Apart from the normal scope for gas-turbine major inspections, significant repair work was carried out to the exhaust systems, thus completing the overall strategy of addressing the exhaust ducting. An extensive inspection programme was developed and executed with the assistance of a technical expert to ensure compliance with the PSSR 2000. The operation certificate was issued for a period of 50 months, the maximum allowed under the regulations.
An important activity was the successful completion of the chemical clean of the HP evaporators’ internal surfaces, and it is believed that this is the first time such a task has been carried out in the UK fleet of unfired HRSGs.
The steam turbine major inspection included removal of the LP rotor last-stage blade front and rear for stress corrosion cracking inspections, followed by high speed balance of the LP and HP rotor. The ST generator rotor, which was also inspected for slot liner migration, was found to be in acceptable condition, thus addressing one of the main risk factors.
Safety
Management of safety was an important aspect of outage preparation. The overhaul was conducted under the CDM Regulations by which a site specific H&S Plan was developed and communicated to all contractors.
A total of 375 safety inductions were carried out. At the peak of activities, a total workforce of around 340 people was on site. It is estimated that in excess of 187,000 man-hours were completed without any LTI.
The services of an external safety practitioner were secured in order to maintain a visible presence around site, and ESBI O&M Solutions provided assistance and support in the application of the H&S processes during the outage.
Seven minor accidents, all to contractors, were recorded during the entire overhaul period with 26 near misses and safety improvements also reported.
Quality
A comprehensive quality plan associated with main work packages was put in place. A team of four engineers from ESBI Engineering, based on site, monitored and ensured effective plan implementation. Additional quality checks and audits were developed with the assistance of ESBI Engineering.
Delivery within budget
Due to the technical challenges posed by adverse findings in the gas turbine compressors, extra time was taken to develop and validate the technical repair solution. A robust and long-term repair was chosen against a temporary solution.
Additional time was required to achieve water/steam chemical purities as prescribed in the operating procedures following the boiler chemical clean.
The plant has now fully returned to service and, when called to run, has not missed a start, achieving an availability rate of 99%.
The major overhaul was completed within the allocated budget.
Speaking about successful completion of the overhaul, Independent Generation Manager Mick O’Mahony said, “Corby staff, contractors and head office support have worked hard and with tremendous flexibility, professionalism and dedication to deliver this challenging programme. The successful outcome could not have been achieved without their commitment and co-operation, for which I thank each person involved.”
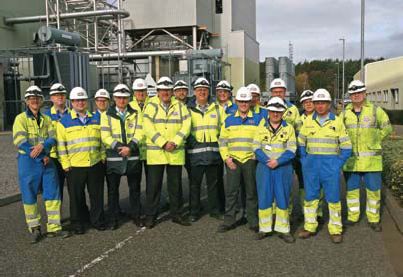
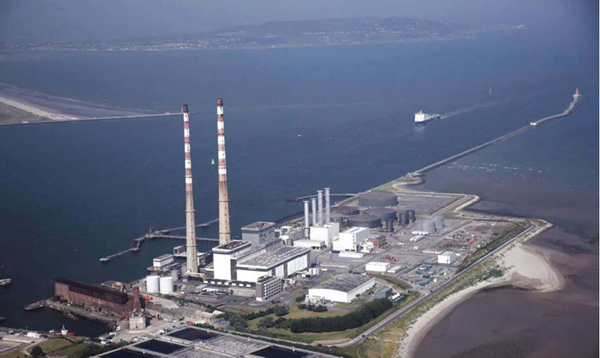
Poolbeg CCGT Mid-Life Refurbishment
2011 was a particularly important year in the life of Poolbeg Combined Cycle Gas Turbine (CCGT) power plant with the completion of the Mid-Life Refurbishment Overhauls – the most extensive overhaul programme in the station’s history.
Poolbeg in brief
Poolbeg CCGT was developed between 1993 and 2000. The plant consists of two 150MW gas turbines exhausting into two heat recovery boilers which in turn drive a 170MW steam turbine, giving a total output of 470MW.
Minor inspections of the gas turbines are scheduled every 8,000 EOH (Equivalent Operating Hours) with major inspections every 33,000 EOH. Each gas turbine had clocked up 100,000 EOH and, therefore, were due major inspections and overhauls in 2011. The recommended major inspection interval for the steam turbine is also 100,000 hours, thus, this too was scheduled for major inspection in 2011. This would be the first occasion the high pressure turbine, which operates at 527oC and 80 bar, was opened up for inspection.
Safety at the forefront
The most important value for the Poolbeg overhaul was safety. Planning for a safe overhaul included a pre-overhaul safety conference which was attended by and included presentations from representatives of all contractors. Siemens, as the main contractor, used the conference to demonstrate their ’Zero Harm’ philosophy, while at the same time Poolbeg set out their expectations of contractors as ‘safety partners’.
A key feature was a continuous safety presence on site by the Safety Advisor with support from project, station and ESBI staff. It was important that this was not seen as a policing role trying to catch staff out, rather to encourage ownership of safety – their own and their colleagues. The Site Safety Adviser was never seen as a threat but instead as a helpful resource.
Other initiatives included ‘Point of Work’ risk assessments, daily safety coordination meetings which were a particular success, and an extensive quality management system with rigorous weekly meetings.
The results speak for themselves – no lost-time injuries (LTIs) with